Las baterías de iones de Litio, las utilizadas por los actuales vehículos eléctricos en todo el mundo, tienen su propio proceso de fabricación. En este informe conoceremos al detalle todos los pasos que se deben seguir para construirlas.
Raúl Moreno, un consultor y asesor de la industria automotriz en vehículos eléctricos de origen español, pero que vive en México, realizó una nota muy completa en Linkedin donde cuenta cada detalle de este importante proceso (leer informe abajo).
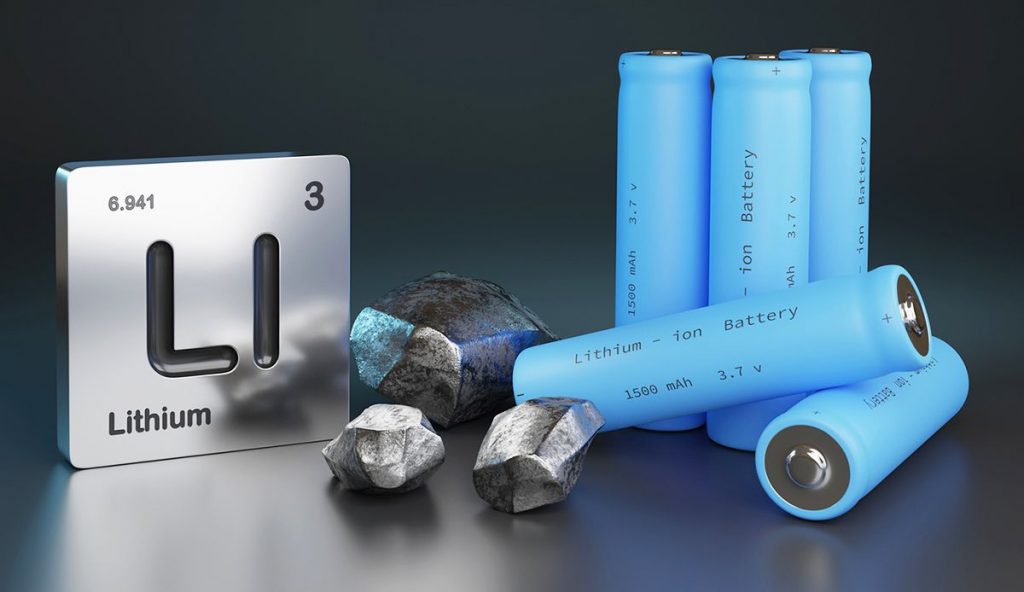
EL INFORME DE RAÚL MORENO:
Fabricación de baterías de Litio:
Introducción:
El desarrollo y la producción de paquetes de baterías de iones de litio son fundamentales en la era de la movilidad eléctrica y el almacenamiento de energía. Los paquetes de baterías combinan celdas individuales, componentes electrónicos y mecanismos de protección que forman un sistema integral y seguro para suministrar energía. Este artículo analiza detalladamente los pasos clave en el proceso de fabricación de estos paquetes, desde la selección y agrupación de celdas hasta el empaquetado final.
Selección y agrupación de celdas:
El primer paso en la fabricación de paquetes de baterías de iones de litio es la selección y agrupación de celdas. Este proceso es fundamental para garantizar la consistencia y la eficiencia del paquete final. Las celdas se seleccionan en función de varias variables, como resistencia interna, resistencia de polarización, voltaje en circuito abierto, capacidad nominal, eficiencia de cargadescarga y tasa de autodescarga.
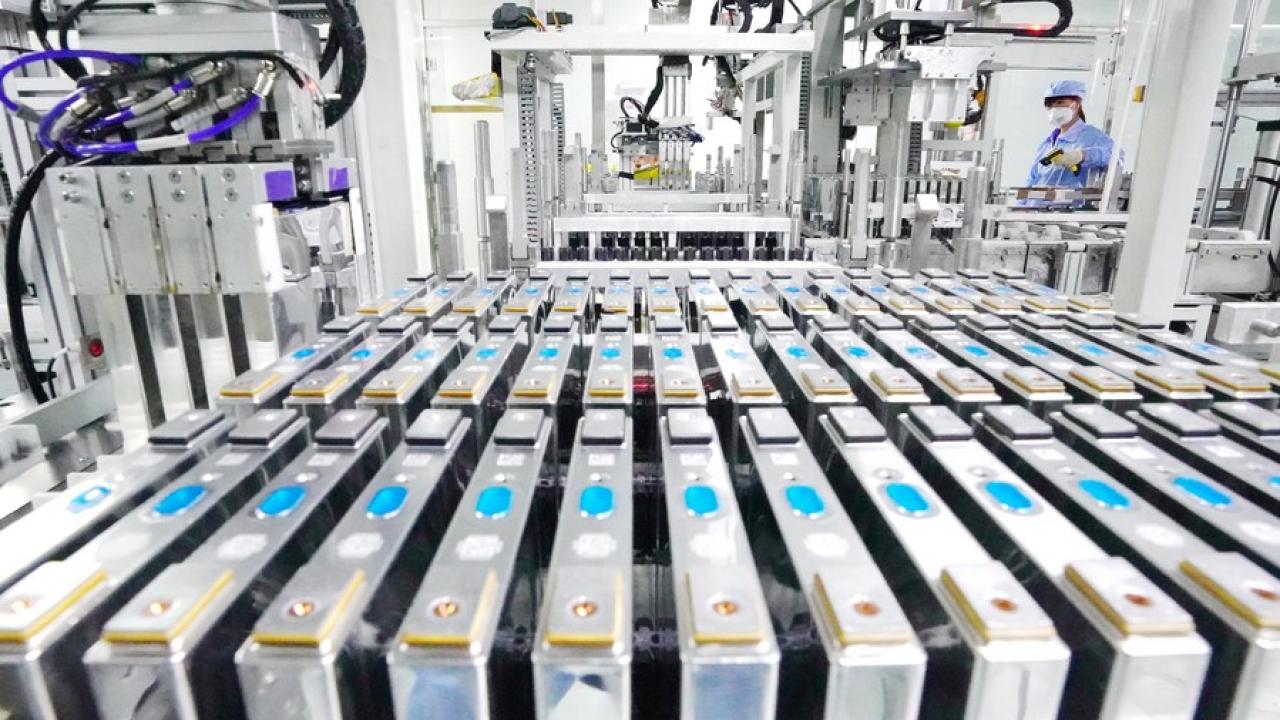
Pruebas y clasificación de celdas:
- 1) Prueba de capacidad de la celda: Las celdas se instalan en equipos de detección para someterse a ciclos de carga y descarga. Este proceso se realiza repetidamente para asegurar que las celdas operen dentro de los parámetros establecidos. La prueba de capacidad se lleva a cabo cargando y descargando la celda varias veces para medir su capacidad efectiva y verificar su consistencia.
- 2) Registro de parámetros: Durante las pruebas, se registran parámetros clave como la capacidad de descarga y los tiempos de carga. Estos datos son esenciales para agrupar celdas con características similares, asegurando que cada grupo tenga un rendimiento homogéneo.
- 3) Clasificación de celdas: Basándose en los resultados de las pruebas, las celdas se clasifican y agrupan para asegurar que cada grupo tenga características homogéneas. La clasificación puede ser por un solo factor, múltiples factores o métodos dinámicos que consideran múltiples variables simultáneamente.
Emparejamiento de Celdas:
- 1) Configuración preliminar: Las celdas con capacidad calificada y parámetros similares se agrupan preliminarmente. Esta etapa implica organizar las celdas en grupos que maximicen la eficiencia y minimicen las diferencias de rendimiento entre ellas.
- 2) Caída de voltaje: Se mide la caída de voltaje de las celdas después de almacenarlas por un período, seleccionando las que cumplen con los estándares de reducción de voltaje. Este paso es crucial para asegurar que las celdas mantengan su carga durante el almacenamiento.
- 3) Configuración Final: Las celdas que cumplen con todos los criterios se emparejan definitivamente para formar módulos coherentes y eficientes. Esta etapa finaliza el proceso de agrupación y asegura que cada módulo funcione de manera óptima.
Equipos de prueba de baterías de Litio:
El equipamiento utilizado en la fabricación de paquetes de baterías es crucial para asegurar la calidad y seguridad del producto final. La automatización y precisión de estos equipos son esenciales para evitar defectos y asegurar el rendimiento óptimo de las baterías.
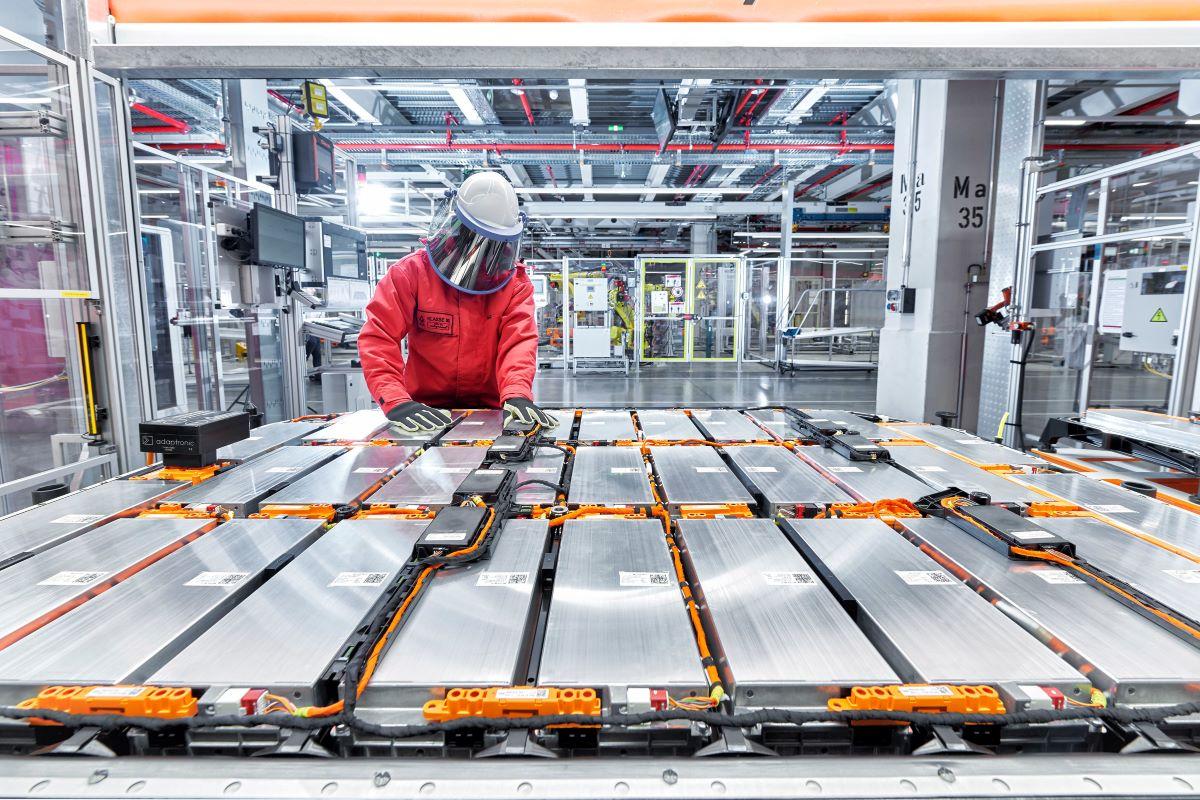
Proceso de ensamblaje:
- 1) Instalación de Celdas: Las celdas se ensamblan siguiendo un procedimiento específico para evitar cortocircuitos, asegurando que los electrodos positivo y negativo estén correctamente alineados. Este proceso requiere atención meticulosa para evitar errores que puedan afectar la seguridad y eficiencia del paquete.
- 2) Soldadura Automatizada: Las celdas se sueldan mediante máquinas de soldadura automatizada que garantizan precisión y consistencia. Después de la soldadura, se inspeccionan las celdas para detectar posibles defectos y se resuelden si es necesario. La soldadura precisa es fundamental para asegurar conexiones eléctricas seguras y duraderas.
Soldadura de PCMBMS:
El módulo de circuito protector (PCM) o el sistema de gestión de baterías (BMS) es el componente central que garantiza la seguridad y eficiencia del paquete de baterías. Estos sistemas protegen las baterías de sobrecargas, sobredescargas y cortocircuitos.
Tipos de PCMBMS:
- 1) PCM con Función de Equilibrio Utilizado en paquetes de baterías de bajo voltaje, ayuda a mantener el equilibrio entre las celdas, prolongando su vida útil. Este tipo de PCM es adecuado para aplicaciones donde la estabilidad y la longevidad del paquete son críticas.
- 2) BMS Avanzado Utilizado en paquetes de alto voltaje, monitorea el rendimiento de cada celda para asegurar una operación segura y eficiente. Los BMS avanzados proporcionan un monitoreo detallado y controlan variables críticas como la temperatura, el voltaje y la corriente de cada celda.
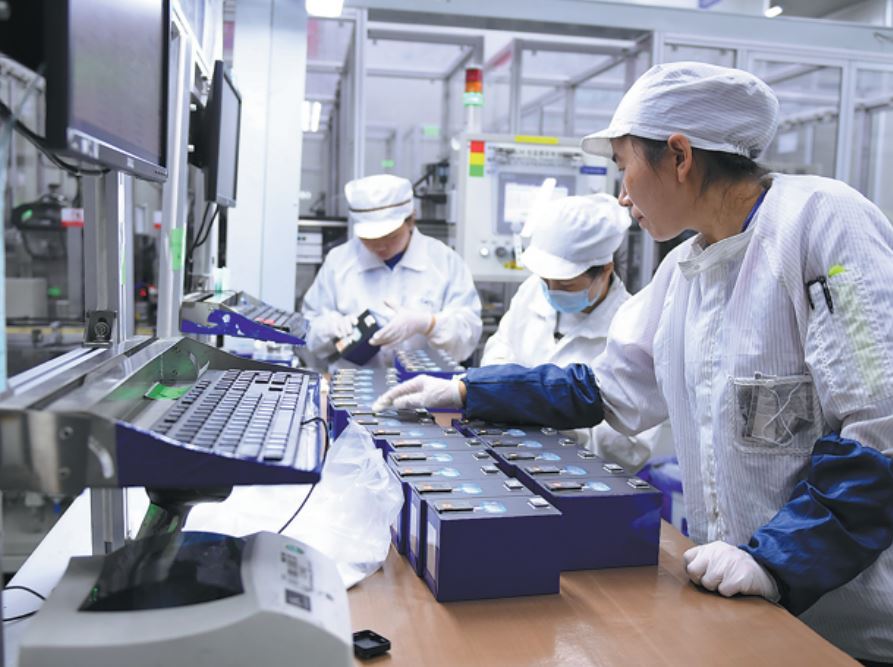
Proceso de integración:
- 1) Inspección de conexiones: Se verifica la calidad de las conexiones de soldadura y tornillos para garantizar una unión sólida y segura. La inspección meticulosa de cada conexión asegura que no haya puntos débiles que puedan fallar durante el uso.
- 2) Soldadura del PCMBMS: Dependiendo del diseño del paquete, se suelda el PCMBMS al conjunto de celdas, asegurando que todas las conexiones sean robustas y sin defectos. Este proceso requiere precisión y experiencia para asegurar una integración perfecta.
Aislamiento y pruebas semiacabadas:
Una vez ensamblado el paquete de baterías, se procede a su aislamiento y a la realización de pruebas preliminares para asegurar que el producto semiacabado cumple con los estándares de calidad.
Proceso de aislamiento:
Fijación de cables: Los cables de adquisición de voltaje y las líneas de salida se fijan y aíslan adecuadamente utilizando materiales resistentes a altas temperaturas y otros elementos auxiliares como papel de cebada y placas de epoxi. Este paso es crucial para evitar cortocircuitos y asegurar la integridad eléctrica del paquete.
Pruebas semiacabadas:
- 1) Pruebas de rutina: Incluyen carga y descarga simple, prueba de resistencia interna, capacidad, sobrecarga, sobredescarga, cortocircuito y sobrecorriente. Estas pruebas aseguran que el paquete funcione correctamente bajo diversas condiciones.
- 2) Pruebas especiales: Se realizan pruebas adicionales como de alta y baja temperatura, acupuntura, caída y pulverización de sal para asegurar que el paquete de baterías pueda soportar condiciones extremas. Las pruebas destructivas se realizan aleatoriamente para asegurar que cada lote cumpla con los estándares de calidad.
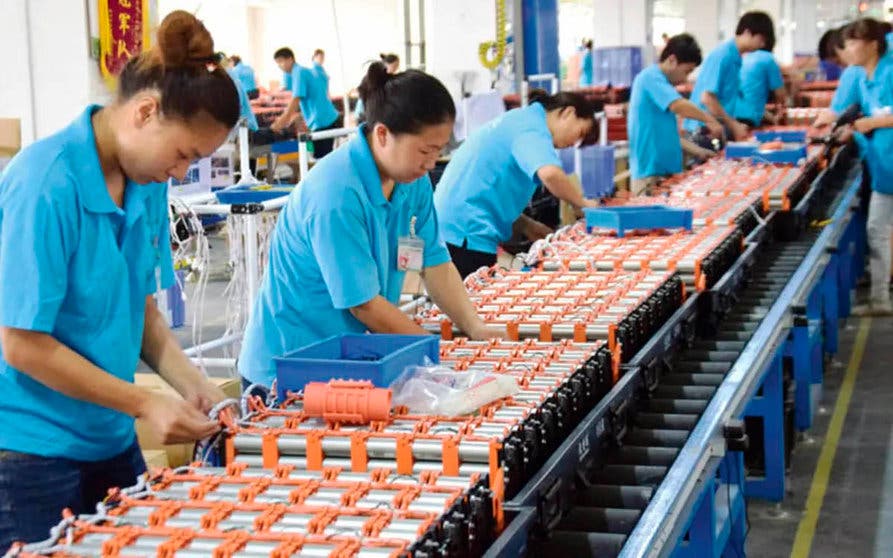
Empaquetado del paquete de baterías:
El empaquetado final del paquete de baterías depende de su diseño específico. Este proceso es crucial para proteger el paquete durante su transporte y uso.
Proceso de empaquetado:
- 1) Preparación del Paquete: Antes de empaquetar, se completan las líneas de recolección de señales y se asegura el aislamiento adecuado de los electrodos positivos y negativos. Este paso asegura que el paquete esté listo para su uso final.
- 2) Métodos de empaquetado: -Encogimiento de Calor: Utilizado para paquetes con revestimiento de PVC. Este método utiliza una máquina de encogimiento de calor para sellar el paquete de manera segura. -Sellado ultrasónico: Proceso realizado en máquinas ultrasónicas para paquetes con métodos de sellado ultrasónico. Este método asegura un sellado hermético y seguro. -Caja exterior de metal: Los paquetes con caja exterior de metal se ensamblan en su caja protectora, asegurando un manejo delicado para evitar daños. La caja de metal proporciona una protección robusta contra impactos y condiciones ambientales adversas.
Conclusión:
El proceso de fabricación de paquetes de baterías de iones de litio es complejo y requiere precisión en cada etapa para asegurar la calidad y seguridad del producto final. Desde la selección y agrupación de celdas hasta el empaquetado final, cada paso es crucial para la eficiencia y longevidad del paquete de baterías. La automatización y el control de calidad juegan un papel fundamental en la producción de estos paquetes, que son esenciales para aplicaciones en movilidad eléctrica y almacenamiento de energía.
Información adicional sobre la fabricación de baterías de litio:
Innovaciones en el proceso de fabricación:
- 1) Tecnología de electrodo sólido: Las baterías de estado sólido están emergiendo como una alternativa prometedora a las baterías de iones de litio tradicionales. Estas baterías utilizan un electrolito sólido en lugar de uno líquido, lo que mejora la seguridad y la densidad de energía.
- 2) Materiales avanzados: La investigación continua en materiales para ánodos y cátodos está llevando al desarrollo de baterías con mayor capacidad y vida útil. Por ejemplo, los ánodos de silicio tienen una capacidad de almacenamiento mucho mayor que los de grafito.
- 3) Procesos de manufactura automatizados: La automatización avanzada y el uso de inteligencia artificial en la fabricación están mejorando la eficiencia y reduciendo los costos. Las fábricas inteligentes pueden monitorear y ajustar automáticamente los parámetros de producción para optimizar el rendimiento y la calidad.
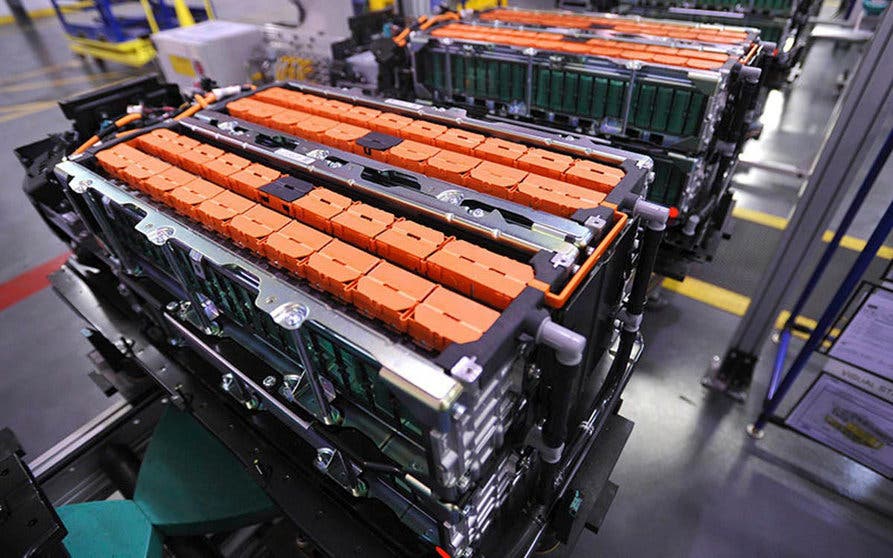
Consideraciones ambientales:
- 1) Reciclaje de baterías: Con el aumento en el uso de baterías de litio, el reciclaje se está convirtiendo en una preocupación importante. Las baterías recicladas pueden recuperar materiales valiosos como el litio, el cobalto y el níquel, reduciendo la dependencia de la minería.
- 2) Impacto ambiental: A medida que aumenta la producción de baterías de litio, es crucial abordar el impacto ambiental de su fabricación y disposición final. El uso sostenible de materiales, la eficiencia en el proceso de fabricación y el reciclaje adecuado son clave para minimizar el impacto ambiental.
- 3) Gestión de residuos: El manejo adecuado de los residuos de baterías de litio es fundamental para prevenir la contaminación del suelo y el agua. Las baterías usadas deben ser recicladas en instalaciones especializadas para evitar la liberación de sustancias tóxicas.
Avances futuros en la fabricación de baterías de litio:
- 1) Nanotecnología: La aplicación de nanomateriales en la fabricación de baterías de litio tiene el potencial de aumentar significativamente su capacidad y vida útil. Los nanomateriales pueden mejorar la conductividad eléctrica y la estabilidad de las celdas, lo que lleva a un rendimiento mejorado.
- 2) Baterías flexibles: La investigación en baterías flexibles está abriendo nuevas posibilidades en términos de diseño y aplicaciones. Estas baterías pueden integrarse en dispositivos portátiles, ropa inteligente y otros productos que requieren flexibilidad.
- 3) Almacenamiento a gran escala: El desarrollo de baterías de litio para aplicaciones de almacenamiento de energía a gran escala, como en redes eléctricas inteligentes y sistemas de energía renovable, está avanzando rápidamente. Estas baterías ayudarán a mejorar la eficiencia y la confiabilidad de las redes eléctricas.
Conclusiones Finales:
El proceso de fabricación de paquetes de baterías de litio es una combinación de tecnología avanzada, precisión y cuidado ambiental. A medida que la demanda de vehículos eléctricos y soluciones de almacenamiento de energía sigue creciendo, es fundamental seguir innovando en el proceso de fabricación para mejorar la eficiencia, la calidad y la sostenibilidad de las baterías de litio. Los avances tecnológicos y las prácticas ambientales responsables son clave para el futuro de la movilidad eléctrica y el almacenamiento de energía.
Para leer más informes de Raúl Moreno, deben ingresar a sus redes sociales: LINKEDIN – INSTAGRAM – YOUTUBE.